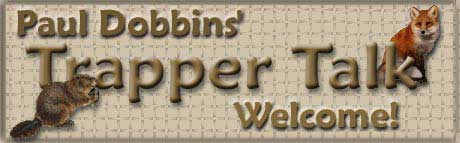

No Profanity *** No Flaming *** No Advertising *** No Anti Trappers ***NO POLITICS
No Non-Target Catches *** No Links to Anti-trapping Sites *** No Avoiding Profanity Filter
Home~Trap Talk~ADC Forum~Trap Shed~Wilderness Trapping~International Trappers~Fur Handling
Auction Forum~Trapper Tips~Links~Gallery~Basic Sets~Convention Calendar~Chat~ Trap Collecting Forum
Trapper's Humor~Strictly Trapping~Fur Buyers Directory~Mugshots~Fur Sale Directory~Wildcrafting~The Pen and Quill
Trapper's Tales~Words From The Past~Legends~Archives~Kids Forum~Lure Formulators Forum~ Fermenter's Forum
~~~ Dobbins' Products Catalog ~~~
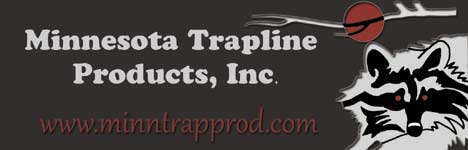
Please support our sponsor for the Trappers Talk Page - Minnesota Trapline Products
|
|||||||||||||||||||||||||||
|
|||||||||||||||||||||||||||
|